Efficient Business Solutions: Outsourcing Plastic Card Production
Table of Contents [ ]
- Outsourcing Plastic Card Production
- Understanding Outsourcing in Plastic Card Production
- In-House Production: The Benefits of Direct Control
- Balancing Costs & Quality: Merging Both Worlds
- Outsourcing Services: When It Makes Sense for Plastic Card ID
- Commitment to Quality and Service Nationwide
- Connect with Plastic Card ID for Your Plastic Card Needs
Outsourcing Plastic Card Production
Outsourcing vs. In-House Production: A Strategic ConsiderationThe debate on outsourcing versus in-house production has been a longstanding one within various industries, and when it comes to plastic card production, this decision is crucial. Plastic Card ID recognizes that the heart of this strategic consideration lies in finding the sweet spot between optimizing costs and ensuring top-notch quality control.
Understanding Outsourcing in Plastic Card Production

Outsourcing involves hiring third-party vendors to handle specific business operations that could otherwise be performed in-house. One of the primary advantages of outsourcing is that it can potentially reduce production costs. considers outsourcing as a viable option to leverage the economies of scale and expertise that specialized vendors offer.
It is vital to gauge if the cost savings justify the shift in production strategies. Outsourcing might also bring forth enhanced technical capabilities that go beyond what is feasible within our in-house resources. It's a strategic move that could radically improve the quality and variety of plastic cards available to our clients.
Advantages of Outsourcing
Outsourcing can lead to significant advantages, here are a few to consider:
- Cost Reduction: By outsourcing, companies can save on overhead costs such as equipment, facilities, and personnel.
- Access to Expertise: Partners specializing in plastic card production often have a depth of knowledge and technological capability that is hard to replicate in-house.
- Scalability: During peak seasons, scaling up production with an outsourcing partner can be more efficient than in-house operations.
The Potential Drawbacks
When considering outsourcing, potential drawbacks must not be overlooked:
- Quality Concerns: There's a risk that the third-party's quality standards may not align with Plastic Card ID 's stringent requirements.
- Communication Hurdles: Working with an external partner can introduce communication challenges that might affect project timelines and outcomes.
- Less Control: There's inherently less control over the manufacturing process and lead times when it's in the hands of a third party.
Why Choose Outsourcing?
Deciding to outsource is based on several factors that companies should evaluate thoroughly:
- Current Production Needs: If the demand for plastic cards is substantial and fluctuating, outsourcing might provide the necessary flexibility.
- Cost-Benefit Analysis: Evaluating the cost savings against the potential risks can help in making an informed decision.
- Strategic Focus: By outsourcing, companies can focus on core business areas like marketing and customer service while leaving production to experts.
In-House Production: The Benefits of Direct Control
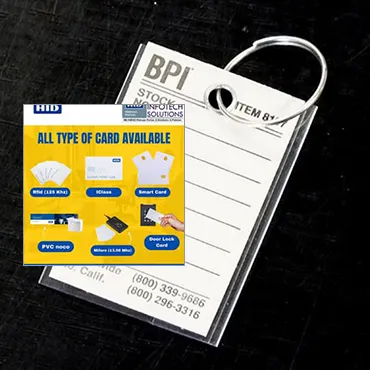
In contrast to outsourcing, in-house production means that all operations related to the manufacturing of plastic cards are conducted within the company. This can translate into a higher level of control over the quality of the product, allowing to closely monitor and fine-tune the production process to meet the exact standards our clients expect.
Having our production facilities means we have the flexibility to tailor orders, make quick changes, and ensure sensitive data remains secure. This direct oversight is paramount in maintaining the integrity and quality of our products.
Quality Assurance
Maintaining production in-house offers a significant advantage in quality control:
- Immediate Oversight: Real-time monitoring of the production process to promptly address any quality issues.
- Customization: Ability to customize orders to the precise specifications of our clients.
- Consistency: Uniformity in production can lead to consistent, high-quality end products.
Data Security
When the production is internal, there's a tighter grip on data security:
- Information Protection: Handling sensitive customer data with the highest level of security can prevent breaches.
- Confidentiality: Keeping all processes in-house ensures that confidential information is not at risk of external exposure.
- Compliance: Ensuring full compliance with industry standards and regulations becomes more straightforward when managed internally.
Challenges of In-House Production
Despite the benefits, there are challenges associated with producing in-house:
- Higher Initial Investment: Cost of setting up a production facility can be substantial.
- Resource Allocation: Resources must be devoted to manage and maintain the production lines, which could be used elsewhere.
- Limited Scalability: Expanding production capacity often requires significant time and capital investment.
Balancing Costs & Quality: Merging Both Worlds
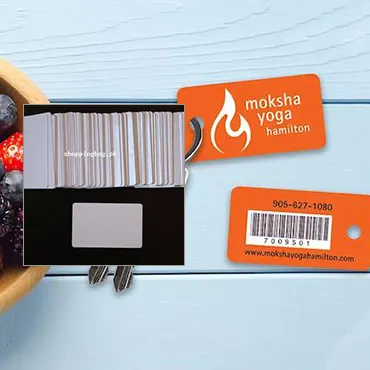
For Plastic Card ID , the ideal situation often lies in a hybrid approach, balancing in-house operations with outsourced solutions. We understand that to provide exceptional service to everyone nationwide, and we must strike a balance between the cost-effectiveness of outsourcing and the quality control of in-house production.
In some cases, we might opt for outsourcing to handle peak production demands or to capitalize on specific technical capabilities that are beyond our in-house scope. Simultaneously, maintaining core production activities in-house enables us to assert stringent quality control over our plastic card products.
Hybrid Model Advantages
Employing a hybrid production model comes with advantages that can benefit both the company and our customers:
- Flexibility: We can navigate through varying demand levels without compromising on quality or delivery times.
- Best of Both Worlds: Leveraging the cost savings of outsourcing while maintaining the critical aspects of control and quality with in-house production.
- Competitive Edge: This approach can provide a competitive advantage, offering both affordability and high-quality products.
Ensuring Seamless Integration
Integrating outsourced services with in-house operations is key to a successful hybrid model:
- Strong Relationships with Vendors: Fostering robust partnerships ensures that outsourced tasks meet our high standards.
- Transparent Communication: Establishing clear communication channels between in-house teams and external vendors is crucial to align all production efforts.
- Continuous Improvement: Constantly assessing and improving the integration process helps to eliminate bottlenecks and streamline production.
Monitoring Costs Closely
It's essential to keep a close eye on costs when managing a hybrid production model:
- Regular Cost Analysis: Periodic reviews of all production-related expenses to ensure competitiveness and cost-efficiency.
- Value Assessment: Comparing the value gained from outsourcing and in-house capabilities to determine the best allocation of resources.
- Strategic Investments: Making smart investments in technology or equipment that can improve in-house production over time.
Outsourcing Services: When It Makes Sense for Plastic Card ID
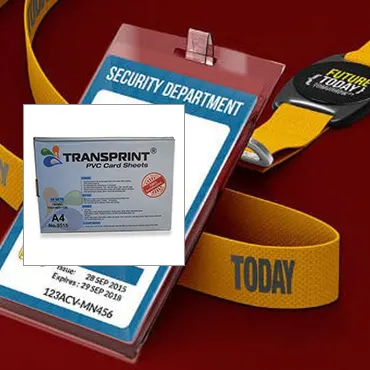
There are specific scenarios when outsourcing services for plastic card production makes perfect sense for us to deliver the best possible products to our clients, no matter where they are located. Outsourcing is particularly advantageous when specialized skills, such as advanced printing techniques or electronic data encoding, are required for a project.
Moreover, when the demand spikes beyond the current capacity of our in-house facility, it becomes necessary to look outward to meet delivery timelines without sacrificing quality. This ensures across the nation, everyone can experience the excellence that is known for.
High-Specialization Projects
Outsourcing is ideal for high-spec projects:
- Specialized Technology: Access to cutting-edge printing and encoding technology that may not be available in-house.
- Expertise: Leveraging the specialized skills of experts in the industry can enhance our product offerings.
- Innovative Features: Outsourcing allows us to incorporate innovative features into our plastic cards that require niche expertise.
Managing Demand Surges
To satisfy demand surges, outsourcing can be pivotal:
- Scalability: Swiftly increasing production capacity through outsourced partners to meet customer demands.
- Timely Delivery: Ensuring all orders are fulfilled on time, maintaining customer satisfaction.
- Cost Management: Controlling costs effectively during peak production periods.
Outsourcing as a Strategic Action
Viewing outsourcing as a strategic action requires thoughtful consideration:
- Long-Term Planning: Determining when to outsource based on long-term production forecasts.
- Strategic Partnerships: Establishing strong relationships with suppliers to ensure responsive and efficient outsourcing.
- Quality Assurance Measures: Implementing strict quality checks even when outsourcing to maintain our high-quality standards.
Commitment to Quality and Service Nationwide
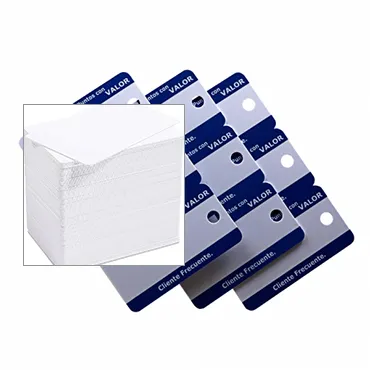
At Plastic Card ID , our commitment to providing high-quality plastic card products remains unwavering, whether the production is in-house or outsourced. We understand that nationwide service means we need to be agile, responsive, and customer-focused. Whether you require a new order or have any questions, please feel free to reach out to us at 800.835.7919 , and we'll be happy to assist you.
For us, our nation's reach is a promise a promise to deliver top-tier products and attentive customer service, regardless of your location. We invite you to experience the reliability and excellence that our clients have come to expect from .
Nationwide Reach with a Personal Touch
Providing nationwide service while maintaining a personal touch is what sets Plastic Card ID apart:
- Nationwide Delivery: We ensure that all customers, regardless of their location, receive their orders promptly and efficiently.
- Personal Customer Service: Our team is always ready to address your queries and provide assistance with a personal touch.
- Consistent Quality: Whether your order is produced in-house or through our trusted outsourcing partners, you can expect consistent quality.
Ensuring Customer Satisfaction
Customer satisfaction is a cornerstone of our business philosophy:
- Feedback and Improvement: Customer feedback is used to continually improve our products and services.
- Tailored Solutions: We aim to provide solutions that meet the individual needs of each client.
- Dependable Support: Our support team is committed to resolving any issues quickly and effectively.
Sustainable Practices
Our responsibility extends beyond just quality control to encompass sustainable practices:
- Environmental Considerations: We strive to use environmentally conscious materials and processes.
- Energy Efficiency: Our in-house production efforts focus on minimizing energy consumption.
- Responsible Outsourcing: We only partner with suppliers who share our commitment to sustainability.
Connect with Plastic Card ID for Your Plastic Card Needs
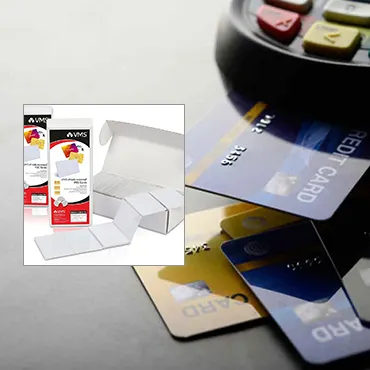
When you choose Plastic Card ID , you're not just getting a plastic card producer; you're partnering with a team that is dedicated to excellence in every aspect. No matter where you are in the nation, we are just a call away to meet your plastic card needs with the utmost attention to quality, cost, and customer satisfaction.
Ready to place an order or have a question? Contact us at 800.835.7919 . Let us be the solution to your plastic card requirements and experience the difference that a strategic balance of in-house and outsourcing production can offer.
The Difference
Our mission is to deliver the best quality plastic cards with unparalleled customer service:
- Reliable Production: We ensure that every card is produced with precision and care.
- Customer-Centric Approach: Fulfilling your needs is our top priority.
- Nationwide Service: Serving every customer across the country with the same dedication to excellence.
Seamless Ordering Process
We make the ordering process efficient and user-friendly:
- Simple Ordering: Our straightforward process makes it effortless to place new orders.
- Consultative Approach: We guide you through the options to ensure you get the perfect solution.
- Customer Support: Our support team is always ready to help should you have any queries or concerns.
Get In Touch with Us
For any inquiries or to initiate your order, reach us at 800.835.7919 . Our team is eager to provide you with exceptional service and high-quality plastic cards to fulfill all your needs.
At Plastic Card ID , we blend the best of in-house control with the strategic utilization of outsourcing to bring you cost-effective, high-quality plastic card solutions. Call us today, and let's start crafting the plastic cards that will elevate your brand and delight your customers.
Previous Page